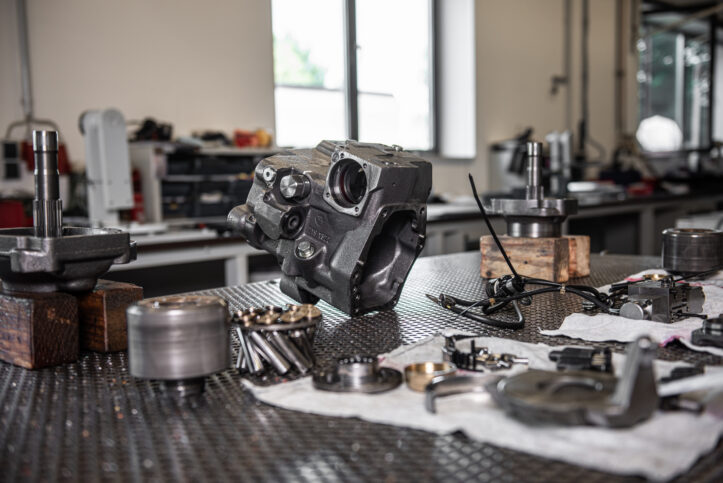
Das GRANIT Service Center hat sein Angebot im Juni 2022 mit der Übernahme der Jetschke Hydraulik GmbH aus Hamburg erweitert.
Mehr lesenIn the industrial area of Weyhe, huge halls and buildings rise into the sky. One of these imposing facilities belongs to the FRICKE Group and houses the production of Hofmeister & Meincke SE - the specialist in tailor-made solutions for commercial vehicle construction.
Hofmeister & Meincke's product range is wide. From three-sided dump trucks and various decking systems, to on-board walls and multifunction boxes, everything is included. Each product is unique, because customers can have their wishes made here.
In fact, most of the customer requests are similar. Just over half of all orders concern the so-called on-board walls. These are the walls of a flatbed that can be folded down to the sides. Also in the "special construction" are products such as multifunction boxes, tippers, or flatbeds. Multifunction boxes are usually located in front of the flatbed and are equipped, for example, with tilting drawers for tools. There are no limits to customer requests at Hofmeister & Meincke. During implementation, a special tool for sales and three engineers support the customer. The customer simply specifies the vehicle, the dimensions and any additional requests, and the work begins.
The advantage of the colleagues in Weyhe is the possibility of working very precisely and quickly using machines. For example, milling or sawing on hinge - which allows you to create an exact angle between several workpieces - requires a lot of experience and the right equipment. For this reason, Hofmeister & Meincke takes care of the fine work and, depending on the customer's requirements, also the assembly of the components into the finished assembly. For instance, an all-frame (lightweight aluminium platform) is supplied, which the customer only has to mount on the vehicle chassis. Alternatively, customers can order the parts as a kit and assemble them themselves.
A good example is the Multiframe III steel floor group for various body systems. The core of the Multiframe III floor groups are the pre-fabricated trusses with integrated cross beam and overhang reinforcements.
As soon as a customer order arrives, the task – in the case of the dashboard – is to design the desired part in the own configurator and create the parts lists. At the same time, the utilization of the workstations is planned. No order can be produced if there is no welding table or workbench available. The planning of the production areas is done via a specially programmed tool, which gives an overview of the resource utilization.
The process from order receipt to delivery in the shipping area can take as little as 45 minutes for a simple side wall with no surface coating. Costs vary greatly as the walls often differ and order quantities are usually low. Often the number of units is 1-4 per order. Smaller batches can also include more than 200 units. For a three-sided dump truck - a flatbed truck whose load surface can be tilted left, right and rear - the processing time is two to three days. Manufacturing is more time-consuming as it has to be accurate to fit and then tested.
The ability to offer tailor-made solutions makes Hofmeister & Meincke a pioneer in the industry. No customer request is too complex, and every order is executed with the utmost precision. In addition to regular products, Hofmeister & Meiincke also takes on challenges: new projects are constantly emerging at trade fairs or in direct contact with customers. This is where the flexibility of the company, which specializes in tailor-made products, pays off. Which products are produced in Weyhe varies from year to year. Its 85 employees, about 50 of whom are in production, are well utilized. Nevertheless, there is potential for development. The products are mostly delivered within Germany, but sometimes also outside the EU.
The warehouses for storage, logistics and production at Hofmeister & Meincke are large, but things are slowly getting cramped, so a new hall is being built to provide air to Hofmeister & Meincke's external warehouse in Arsten. The profiles are stored in two long goods warehouses and by block storage. In the long goods warehouses, two shelf conveyors make efficient use of the compartments. After picking, the profiles go either into processing or directly into packaging.
In the machining process, a "touring saw" waits for the profiles to be cut to fit them. After that, the profiles go "on tour" and are delivered to the customer. Alternatively, they can be taken to the next hall for further processing, where they are assembled into on-board walls or other products.
The trainees in Weyhe also have a responsibility. The workshop area specially designed by the trainees shows how young people are encouraged at Hofmeister & Meincke. Here, the skilled workers of tomorrow come up with creative solutions and improve their skills in design and manufacturing.
A new location of Hofmeister & Meincke is being built in Lindern, near Cloppenburg. The company JW-Tec GmbH, now part of the FRICKE Group, with 14 employees, manufactures vehicle components and load securing systems for wood transporters. These components are delivered to customers for in-house assembly.
Bringing together two companies with different ways of working is an exciting task. The combination of JW-Tec's expertise in cargo securing and Hofmeister & Meincke's expertise in vehicle construction creates new synergies that will benefit both sites. For Hofmeister & Meincke, this is just another challenge that the company will master with its usual precision and flexibility. We look forward to the developments and wish them every success!
Das GRANIT Service Center hat sein Angebot im Juni 2022 mit der Übernahme der Jetschke Hydraulik GmbH aus Hamburg erweitert.
Mehr lesenElena und Steffi sitzen seit fast 20 Jahren im POM. Was POM bedeutet und was die Aufgaben sind, erfahrt ihr hier.
Mehr lesen
Kommentare